When selecting a reciprocating pump valve, it’s important to understand many critical details about the pumping application, including the pressure rating and temperature, viscosity, and composition of the fluid being pumped. Is the fluid corrosive? Will it contain abrasive solids? If so, how large might the particulates be? For example, in some mining applications, it makes more sense to select a pump valve that is engineered to withstand small solids and other abrasive materials.
When we talk about composition of the fluid being pumped, not only are we trying to be cognizant of solids that may end up inside the pump, but also the chemical make-up of the fluid flowing through the pump. In instances where reciprocating pumps operate in oil fields, there can be some occasions where hydrogen sulfide (known as H2S) can be pulled up through the pump unintentionally. Hydrogen sulfide is a naturally occurring substance found in crude deposits that is corrosive, flammable, and poisonous to humans, so it is important to fully understand the chemicals your pump and pump valve may come into contact with. In addition to safety concerns, this gas can corrode pump valves over time, making it essential to choose the right pump valve for longevity, durability, and reliability.
Another factor that affects longevity, durability, and reliability is temperature. Very high temperatures can negatively affect pump valve discs, causing them to become soft and fail prematurely. For temperatures between 180 to 250 degrees Fahrenheit, we recommend using a valve with the disc or valve member material made from metal or Sustakon® – as the Delrin® materials works best for temperatures up to 160 degrees. Keep in mind that pump valves are manufactured to fit specific pumping environments, and when a pump valve is incorrectly selected, it can also cause inefficiencies that result in lost production.
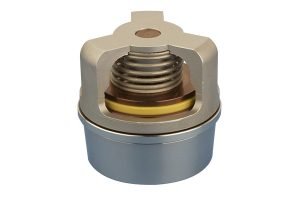
For instance, some of our best customers who have appreciated the long life and durability of our Resista® Abrasion Resistant (AR) Valves have installed them everywhere. We sometimes have to advise our customers that there are cases where it would make sense to use a different pump valve to make sure they take advantage of the highest efficiencies. In cases where clean water is being pumped, there are higher efficiencies (and therefore increased production) that can be achieved if a Durabla® V7F, Durabla® V7FD, or even a PlenaFlow® Plate valve are chosen instead. The Durabla® valve fits the peak mechanical efficiency of the pump and runs at 96% (learn more about that in our whitepaper, titled “Valves that Match the Mechanical Efficiency of Reciprocating Plunger Pumps”).
The purpose of any pump valve is to open and close efficiently between the suction and discharge chamber in unison. If there is “lag time”, it can cause fluid to bleed between cylinders, and the pump won’t run well. We take the speed of the pump into consideration because the industry’s ‘rule of thumb’ is that the higher RPM of the pump, the heavier the spring should be. Now, in cases where there is a low suction issue, or a low NPSHa (net positive suction head available), you should not use a valve with a heavy spring in it – as the valve tends to remain closed. As a result, the pump is starved and cavitation can occur; which damages the pump. There is also the issue of lost production with downtime.
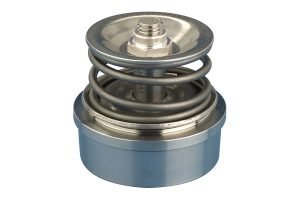
Keep in mind that low pressure issues can happen when suction piping was not designed correctly or if something occurs with the pump’s configuration that results in an NPSH problem. Another issue that frequently occurs is when sediment fills the tank feeding the pump. Over time, this accumulating sediment blocks the suction line. The sediment can also build in the pipe itself and decrease the internal diameter. So in cases where there is a low suction or low pressure issue, we often recommend the Durabla® V7H valve which is engineered with a lighter spring, or the WG Sphera® series which has the option to use a lighter spring. The plate valve can also use a lighter spring and open freely in a low suction pressure problem.
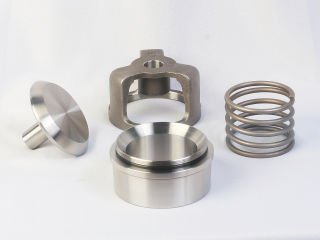
Whatever issue you’re facing, the engineers at Triangle Pump Components Inc. can help you select the right pump valve for your specific needs. We draw on a century of experience to provide you with the most dependable pump components for various applications in many environments. Download our valve comparison chart today or contact us for answers to your questions!