Reciprocating pumps are useful in various applications. These specialized pumps have countless uses, but their main use is to pump liquids.
Below we dive into how reciprocating pumps work, the industries that are best suited to utilize them and the advantages of owning one.
How Does a Reciprocating Pump Work?
Reciprocating pumps are comprised of six basic components. These are:
- A fluid end: The fluid end contains and then displaces liquid in hydraulic applications. The fluid end is divided into two chambers; a larger suction chamber and a smaller volume discharge chamber. These respective chambers have suction valves in the lower suction chamber and discharge valves in the upper discharge chamber. They open and close as the plunger moves back and forth moving liquid under pressure from the suction chamber to the discharge chamber.
- A suction (inlet) pipe: This is the point of entry into the fluid end. A mechanism gradually brings liquid into the fluid end until the fluid end’s chamber is at maximum volume capacity.
- A plunger: A plunger has the task of displacing the compressed liquid inside a reciprocating pump’s suction chamber and subsequently allowing for replacement within the same chamber. The plunger retracts away from the suction chamber as the suction pipe discharges liquid into the suction manifold beneath the suction chamber. Once the suction chamber has reached its maximum capacity for liquid storage, the suction valve closes off, and the plunger begins its forward motion for displacement. As the plunger advances toward the suction chamber, the discharge valve opens, and the liquid in the suction chamber is pushed out and into the discharge chamber. Once the discharge chamber reaches its maximum capacity, the discharge valve closes and the process repeats itself.
- A crankshaft: The crankshaft has a sheave on the end. V-belts connect a large sheave on the crankshaft to a smaller sheave on the motor. This rotates the crankshaft.
- A discharge pipe: This is the delivery channel of the force generated by the liquid displacement toward the desired destination.
- A suction and discharge inlet piping: Liquid is moved into and out of the suction and discharge chambers through suction “inlet” piping and discharge piping.
Why are reciprocating pumps also called positive displacement pumps? Positive displacement pumps, in contrast with centrifugal and non-positive displacement pumps, produce a constant flow at a given speed despite variations in discharge pressure.
Positive displacement pumps have an expanding cavity during suction and a decreasing or collapsing cavity during discharge.
Industries That Use Reciprocating Pumps
A wide range of industries uses reciprocating pumps in diverse applications. Incorporating reciprocating pumps results in repeatable and precise mechanical operations. Industries that commonly use reciprocating pumps include:
- Oil and gas: Oil and gas industry applications include disposal, offshore oil, production, injection, feed, charge, steam generators, mainline, and field gathering.
- Chemical processing: Raw natural gas liquids (NGLs) derived from fracking need to undergo multi-stage processing in order to convert into chemical products such as PVC. Chemical processors frequently use reciprocating pumps for rigorous processing operations.
- Food processing: Reciprocating pumps in the food industry allow for the movement of ingredients from one vat to another, the transportation of liquids of various viscosities, and the delivery of water for food safety and sanitation.
- Mining: The safe and efficient transportation of minerals from mines to processing locations is a key procedure of successful mining operations. Slurry pumps are one critical application in which reciprocating pumps play a large role.
- Paper and pulp manufacturing: Mechanical and chemical pulping processes both use reciprocating pumps that are able to withstand intense operating conditions.
- Soap manufacturing: It takes a lot of processing to transform raw soaps, liquids, and powders into products ready for consumer purchase. Reciprocating pumps are a key component in many of these manufacturing and refining processes.
- Wastewater treatment: Wastewater treatment plants are responsible for contaminant removal, purification processing, and the proper treatment of waste effluent. Reliable and durable reciprocating pumps are extremely important to maintain the effectiveness of a treatment plant’s operations.
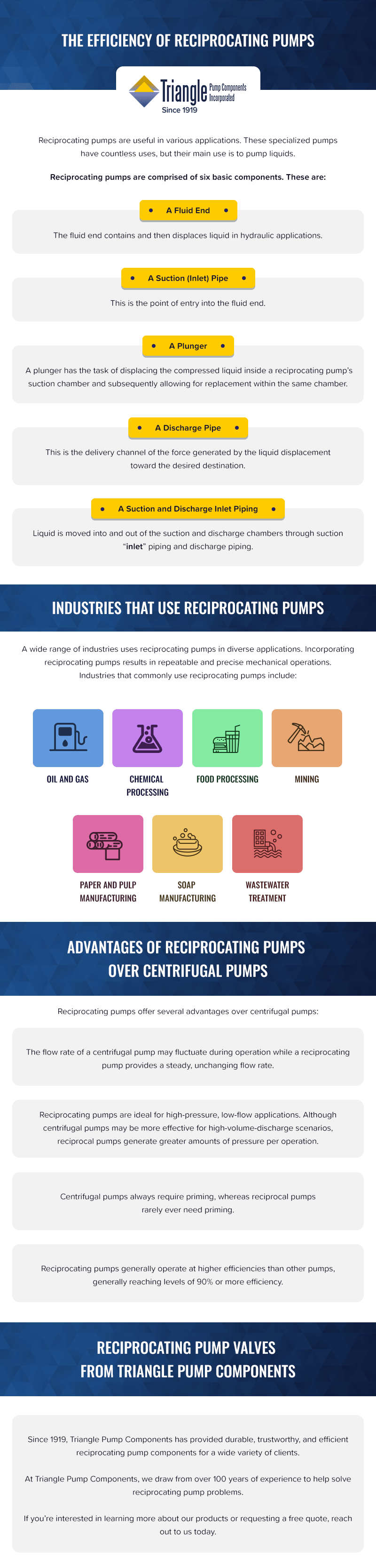
Advantages of Reciprocating Pumps Over Centrifugal Pumps
Reciprocating pumps offer several advantages over centrifugal pumps:
- The flow rate of a centrifugal pump may fluctuate during operation while a reciprocating pump provides a steady, unchanging flow rate.
- Reciprocating pumps are ideal for high-pressure, low-flow applications. Although centrifugal pumps may be more effective for high-volume-discharge scenarios, reciprocal pumps generate greater amounts of pressure per operation. For instance, reciprocal pumps used in water jet cutting applications may generate pressures greater than 10,000 PSI.
- Centrifugal pumps always require priming, whereas reciprocal pumps rarely ever need priming.
- Reciprocating pumps generally operate at higher efficiencies than other pumps, generally reaching levels of 90% or more efficiency.
Does Cavitation Occur in Reciprocating Pumps?
Cavitation, or the formation of bubbles or vapor cavities in a liquid, results from rapid fluctuations in pressure. Cavitation causes shockwaves throughout a pumping system as those bubbles burst, and some of the force of displacement is scattered towards different vectors.
Cavitation can create undesirable noise and vibrations, decrease efficiency, and, over time, reduce your equipment’s life span.
Two basic types of cavitation exist in reciprocating pumps:
Suction cavitation can result from obstructed, clogged, or otherwise dysfunctional inlet pipes. When the inlet pipe’s optimal flow is hampered, vapor cavities form near the retracting plunger. Common causes of suction cavitation include:
- Clogged filters
- Pipe blockages
- Sub-optimal piping design
- Disregard of net positive suction head (NPSH) guidelines
Discharge cavitation is the opposite of suction cavitation. This hampers outward flow from the pump fluid end, causing the formation of cavities from rapidly churning fluid trapped inside the chamber.
Many of the same causes of suction cavitation, such as poor pipe design and clogged filters, can also cause discharge cavitation.
Reciprocating Pump Valves from Triangle Pump Components Inc.
Since 1919, Triangle Pump Components Inc. (Triangle®) has provided durable, trustworthy, and efficient reciprocating pump components for a wide variety of clients.
We serve many different fields of industry, including all those mentioned above. Our product offerings include the following:
- The CavPack® valve set which features the Durabla® V7H and the Durabla® V7F Pump Valves working together to help ensure a consistent flow to prevent cavitation. Companies from a variety of industries use these two valves, including oil and gas companies, food processing companies, and wastewater treatment plants.
- The Resista® Abrasion Resistant (AR) Valve, which is ideally suited for pumping slurry and for use in pumping environments containing small solids, high pressures, and abrasives.
- The double-sprung PlenaFlow® plate valve is capable of pumping ammonia, gasoline, petrochemicals, hydraulic fluid, sulfuric acid, and many other abrasive and corrosive materials while operating under pressures up to 15000 psi.
- The WG Sphera® series boasts the flexibility to work with clean, abrasive, hot or cold fluids. This stem-guided spherical valve’s design includes a radiused valve member that allows for a larger flow area, adequate sealing, and unrestricted flow.
At Triangle®, we draw from over 100 years of experience to help solve reciprocating pump problems.
If you’re interested in learning more about our products or requesting a free quote, reach out to us today.
(Editor’s note: This post was originally published on May 8, 2019 and has been updated for comprehensiveness)